Clean hydrogen is reshaping energy networks demanding advanced metering to tackle billing, infrastructure, and quality challenges. Emerging tech like solid-state sensors is driving innovation, creating new opportunities for manufacturers in a booming market.
The Hydrogen Council says in their Sept Insights report that “Between 2020 and 2024, clean hydrogen supply capacity planned through 2030 has grown from about 7 Mt p.a. in 2020 to 48 Mt p.a. today.”
Clean hydrogen utilises low carbon production techniques such as ‘blue’ carbon capture and ‘green’ production from distributed locations and sources such as electrolysers which are likely coupled to renewable energy sources.
Future users will range from those in industry seeking to decarbonise hydrogen used in their processes, or replace hydrocarbon energy source, to hydrogen powered transportation, to domestic users. Each application has varying needs from pure hydrogen to potentially hydrogen natural gas blends.
As a consequence of this trend, the natural gas industry is contemplating a significant transformation as hydrogen emerges as a viable renewable alternative to natural gas, either in pure form or as a blend-in component to reduce carbon emissions and enhance energy sustainability.
The long history of using hydrogen in industrial processes, for food, chemical, and steel production shows that the movement and measurement of hydrogen can be done safely.
In Germany, the National Hydrogen Strategy seeks to establish a robust hydrogen economy and reduce reliance on fossil fuels:
“The Bundesnetzagentur approved the application on 22 October 2024 with some changes. The approved measures for the hydrogen core network are for a total of 9,040 kilometres of pipelines, around 60% of which are natural gas pipelines that will be converted to hydrogen. The total investment costs are expected to be €18.9bn.”
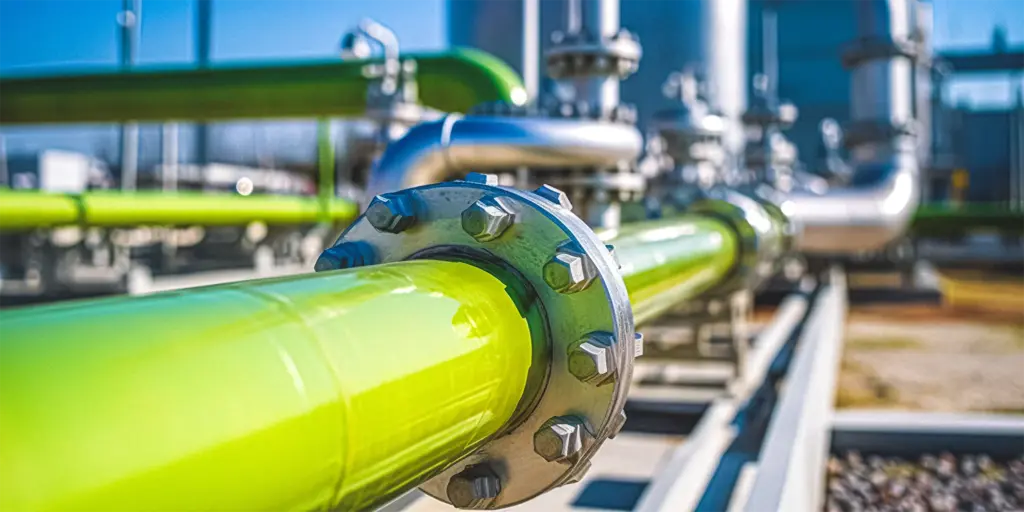
In the UK, transmission and distribution networks are grappling with safety, feasibility and regulatory study and planning aspects. It is likely that hydrogen blends will be supplied to domestic natural gas consumers, which has merit in so far as existing appliance types are likely to be tolerant of blends and in early years, hydrogen production capacity will not be sufficient to replace hydrocarbon fuels entirely.
The infeed of hydrogen and renewable sources of hydrocarbons from distributed production sources introduces complexities for the operation of a commercial market. The ability to measure complex blends for metering and quality analysis is needed in order to maintain the chain of custody for secure and reliable delivery. Further large industrial consumers will need monitoring techniques to enable control for process stability using the gas blend that may vary.
Challenges of metering hydrogen blends
In the UK, Cadent are studying options for Future Billing Methodology Options for natural gas – hydrogen blends – they are considering a range of approaches including working within existing frameworks, online modelling, zonal and local measurement.
Hydrogen’s unique physical and chemical properties- low molecular weight, operating density, and high diffusivity – pose challenges to conventional metering and traceable calibration techniques.
For gas transmission and distribution network operators, precise metering, composition and quality is critical for maintaining the chain of custody:
- Billing: fiscal metering for custody transfer depends on accurate measurements of flow, composition and calorific value (CV) at local ‘governor’ sites to ensure fair pricing for future hydrogen producers, distributors and consumers
- Infrastructure compatibility: hydrogen’s interaction with existing natural gas pipelines and equipment can affect operational safety and efficiency, necessitating continuous monitoring
- Quality assurance: fluctuations in gas quality due to varying hydrogen concentrations contaminants and trace gases impact combustion performance and potentially in the case of contaminants impact consumer equipment
Today, a wide range of flow measurement techniques are applied including turbine, ultrasonic, coriolis, thermal mass and differential pressure, depending on application requirements, and these solutions are in use for hydrogen.
Gas chromatography (GC) instruments are widely used today for detailed compositional analysis of natural gas. However, as hydrogen blends are introduced and the potential sources for hydrogen production proliferates traditional GC methods face limitations.
Limitations of gas chromatography in the future hydrogen economy
Gas chromatography has long been a cornerstone of natural gas analysis, offering high accuracy and detailed separation of gas components. Its ability to identify and quantify hydrocarbons and other compounds has made it indispensable for the petrochemical and natural gas industry.
Despite its strengths, GC systems face challenges in hydrogen applications:
- Measurement speed: GC systems require a sample preparation and analysis cycle time may not meet the need for real-time data for sensing variation of CV in hydrogen blend networks
- Calibration complexity: Frequent recalibration is needed to account for the variability in hydrogen content and gas mixtures
- High total cost of ownership (TCO): GCs are expensive complex instruments to purchase. Maintenance, calibration and operation of GC systems can be resource-intensive requiring specialist personnel. Whilst the high throughput of transmission network might support these costs, smaller volumes in distribution network or at hydrogen production inputs may not
For manufacturers of sensing and metering instruments, these challenges represent an opportunity to innovate and develop new solutions to meet the evolving needs of the hydrogen economy.
Alternative hydrogen sensing approaches
There are a range of hydrogen sensing approaches – physical, solid state and spectroscopic approaches some of which are available in the market, or in development.
GasPT analyser measures physical properties of a sample of gas from which composition is inferred. From the inferred composition Calorific Value, Density, Relative Density and Wobbe index is derived from standard approaches. The technique uses reference tables for inference. The sensor is not in contact with the gas and there is no venting or purging of consumed sample required.
H2Scan Hy-Optima is a platinum solid-state sensor offering high sensitivity, low detection limits, and a rapid response time. The Hy-Optima is particularly valued for its robust performance in harsh environments, offering resistance to temperature fluctuations, humidity, and exposure to other gases, without the need for regular recalibration.
Solid oxide fuel cell (SOFC)-type sensors are an innovative technology for detecting hydrogen due to their high sensitivity, and selectivity. These sensors leverage the electrochemical principles of SOFCs, where a solid electrolyte facilitates the conduction of oxygen ions, enabling the detection of hydrogen through its oxidation at the anode.
The current generated during this process correlates directly with the hydrogen concentration. SOFC sensors are particularly advantageous in industrial settings because they are robust, capable of functioning in harsh environments, and resistant to interference from other gases.
Furthermore, their high operating temperature enhances reaction kinetics, leading to rapid and accurate detection, making them suitable for hydrogen monitoring in energy systems, safety applications, and process control.
Infrared (IR) spectroscopy offers a compelling alternative to traditional gas chromatography. This technique measures the absorption of IR radiation by gas molecules, enabling the rapid identification and quantification of various components. However, this technique is not suitable for sensing of molecular hydrogen which is a homonuclear diatomic and does not absorb near-infrared radiation effectively.
Raman spectroscopy is a powerful tool in the process industry for at-line compositional analysis, enabling real-time monitoring and quality control. This technique uses inelastic scattering of monochromatic light to identify molecular fingerprints, allowing precise determination of chemical composition and structural information. In the process industry, it is particularly valuable for monitoring complex chemical reactions, detecting impurities, and verifying product consistency without requiring extensive sample preparation.
Sensor fusion approach such as the combination of spectroscopy and thermal conductivity has been developed in the Research Project ‘Gas Efficiency’ – RMA Pipeline Equipment
Implications for gas sensing and instrument manufacturers
The integration of hydrogen into natural gas grids marks a turning point for the energy industry, bringing both opportunities and challenges. Accurate metering and quality analysis are essential to ensuring the successful adoption of hydrogen blending.
For gas sensing and instrument manufacturers this trend represents an opportunity for the development of new products to address unmet need and the hydrogen economy grows, and new applications and use cases emerge.
Duncan Lindsay, Director of Industrial Products at 42T says, “For gas sensing and instrument manufacturers, there are several opportunities here: market expansion and revenue growth, competitive differentiation, reduced operational costs, product versatility, sustainability goals, R&D opportunities and futureproofing product offerings, to name a few.
The key is to know where to look for assistance, and who to speak to with regard to research, product development and putting partnerships together which, as a consultancy that deals with many different industries, 42T is well placed to do.”
The UK is also an excellent location for the development of such products with hydrogen equipped test facilities for testing and validation such as:
- Element Materials and Product Testing, Inspection & Certification
- The Spadeadam site FutureGrid | National Gas operated by DNV
- The Gas Network Hydrogen Testing Facility operated by HSE
- The Keele University – HyDEX Demonstrator a Smart Energy Network Demonstrator (living laboratory)
- Hy-One at RGU | Hydrogen Storage Testing Facility at Robert Gordon University
- others for certification such as Kiwa Energy | Hydrogen Appliance Testing Certification
Duncan adds, “We at 42T have a strong track record in industrial capability, particularly in gas measurement and detection, but because we have a well-developed R&D function across several disciplines and sectors all under one roof, our solutions are very often ground breaking and novel. Not only do we achieve results but it’s often a more cost-effective option for clients in terms of managing overheads.”
“With the rise of new technologies, we incorporate cutting edge new developments as they occur and we’re able to integrate AI and machine learning into these. We have first-hand experience of embracing hybrid solutions, enhancing calibration techniques, and collaborating with industry partners, so that our clients can remain at the forefront of this evolving market.”