Dr Peter Brown, a leading expert in printing and packaging, was interviewed by FuturePrint. Here he talks about the innovations in printing technology which have the potential to revolutionise many industries in the future.
To gain an idea of the kinds of technology Peter is well versed in, organiser of the FuturePrint event, Marcus Timson, spoke with Peter about his background, his career in inkjet, and his work at 42 Technology.
Peter explained that his initial interest in industrial inkjet was piqued while studying for a PhD in polymer electronics at Cambridge University. Since then, consulting in technology development has been the focus of his career. Peter estimates that two thirds of his career has been in inkjet.
Right now, Peter’s role at 42 Technology is Director of Industrial, which means he is head of business development in the industrial sector. Peter reflects on the changing inkjet landscape over the past 20 years.
Some background on the industry
“Twenty years ago, inkjet was difficult, and it was new. You needed really smart, multidisciplinary people to create these systems,” he explains, noting that while building print heads is an essential component, what really goes into a printing system is much more complex.
“Since then, the industry has matured and specialist companies have emerged with the expertise to handle drive electronics, fluid supply systems, software, waveforms, and more.”
What does this mean for inkjet?
Peter says, “The need for consultants with PhDs to design a fairly normal system is unnecessary – you don’t need it anymore. However, I think that that has left a gap. There is still space for smart, multidisciplinary people, particularly to help businesses moving into new markets. That’s where we at 42T sit.”
The Cambridge tech hub
As well as assisting businesses entering these new areas on a practical level, 42T also provides independent perspectives for clients navigating the transition from analogue to inkjet, or bringing inkjet printing in-house. When Peter talks about the scope of inkjet applications, he stresses that this goes way beyond traditional realms like decorating. He talks about inkjet technology making in-roads in a variety of sectors such as automotive painting.
Peter positions 42 Technology as assisting companies that may not be in need of extensive multimillion-pound, long-term development but perhaps businesses that have already invested significantly in building their research and development teams, facilities, and capabilities, may require specialised assistance on the periphery of their core expertise for short-term projects as they develop a new product or a new manufacturing process or a new machine.
Peter explains: “We start small, build credibility, and then deliver the heck out of a project. Clients will say, you know what, that was brilliant, can you do the next phase please – and while you’re doing that, actually, we’ve got another project you might want to work on.
It’s very usual to start working with a client on a smallish project, and before you know it, a year or two later, you’re working on three or four parallel projects at the same time and going gangbusters. And our clients love that, they absolutely love it! Because we take the time to build trust and a good relationship with our clients and as a result, we’re growing like crazy.”
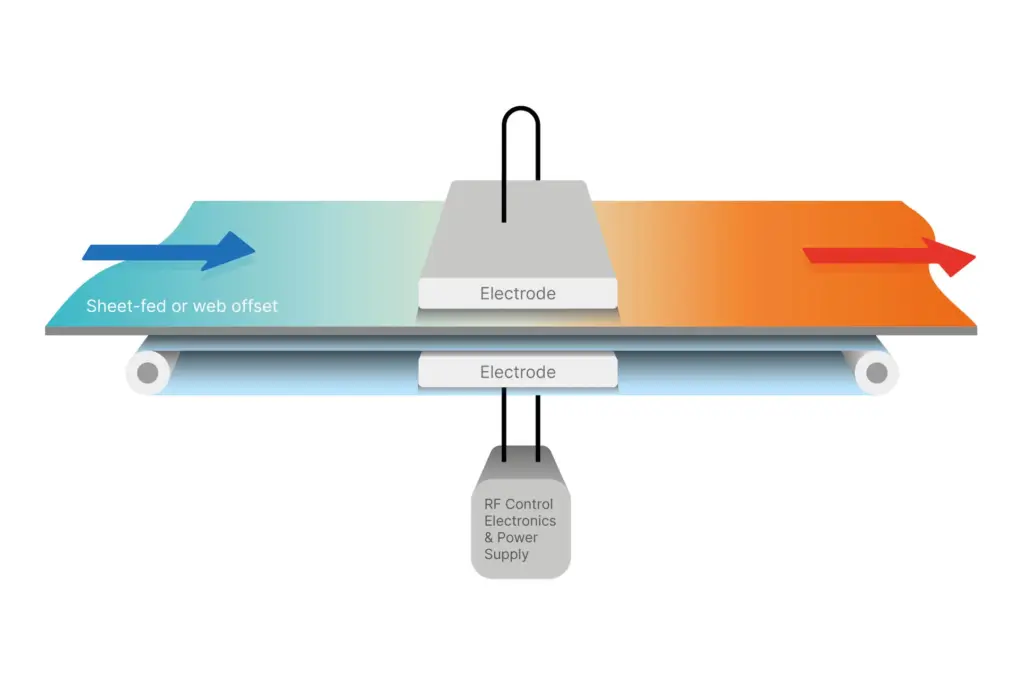
One significant advantage of working with 42T is the ability to accelerate project delivery. The company deliberately limits its concurrent project load, working on a maximum of three or four projects at once, allowing them to prioritise speed.
As well as a swift project execution, Peter says that 42T brings an approach beyond incremental innovation: “In every industry and in every company’s life, at some point time you’ve got to step up and do something radical if you want to stay relevant, or if you want to stay ahead of the competition. The same project management techniques, the same skill sets, the same outlook on life that you use for incremental innovation is not what works.”
“Companies can get away with light-touch project management on step-change projects for a little while; they’ll be working towards a milestone they promised their CEO or a customer, and a goal that they think they’ll definitely hit and suddenly it doesn’t work. 42T understands the risks and pitfalls of step-change project management and we can either help our clients avoid falling into this hole by taking a risk-based approach, or help them to climb out of the hole.”
The future of high-viscosity inkjet
Peter also discusses his years spent developing an inkjet technology that could print high viscosity large particles.
“For years, we were in the lab printing things that we knew nobody else could do anywhere else in the world at that time,” he explains. So why isn’t everyone using this technology now, one may ask? “The answer was that we got it to the point where we needed a £10 million investment in order to build a factory to start churning out these heads to make it a reality – that’s quite a big barrier!”
Peter notes that recent developments have made high viscosity printing a reality, reducing the need for significant initial developments. “You can go and buy the heads, and they will work. This opens up, massively, the chemistry that you can use to make your inks, which means that the functionality that you can deliver with those inks is huge.”
He adds, “It’s no longer merely a low viscosity carrier with some pigments in there. You can develop far better varnishes or adhesives or 3D printing materials. Now, you can print paint, security materials, you can potentially print electronics materials using flakes instead of nanoparticles, for instance, silver. All of these things have been pipe dreams in printing for years. It’s not going to happen overnight, but I’m really excited that ‘off the shelf’ technologies are now available to do high viscosity printing because I think that’s going to open up huge numbers of applications.”
The advent of new tech – RF drying and others
The practical effect of these physical properties is that, in order to dry water-based inks quickly, you need to pump in a lot more energy to initiate evaporation and implement a greater volume of mass transport to remove vapour to keep the water evaporating.
Peter says: “The conventional way of achieving this effect is to blow hot air across the ink. This is an obvious, relatively low-cost way of achieving increased evaporation rates. However, there are some drawbacks.
- It is relatively inefficient – much of the input energy is used to heat air, via a heating element, that has no impact on the temperature of the water.
- This approach heats other objects in the nearby vicinity that could be negatively impacted, particularly the substrate. Many plastic films and other delicate substrates can be easily damaged by unwanted heating.
- The equipment required to heat and blow the air can have a relatively large footprint.
- It can be noisy, particularly for large systems, degrading the working environment.
These drawbacks leave the door open for other heating techniques to be employed, which could be advantageous in the right application. We have examined the physics of evaporation of water droplets in detail and subsequently studied the ways in which heat could be introduced into the droplets.”
A future of customisation, lower costs and sustainability
42T has been working in the area of high viscosity digital deposition for over 10 years and we are uniquely-placed to help companies with this transition. We are experts at process development and have close ties with much of the supply chain, including Xaar.