Soaring energy costs in the last year are significantly affecting many manufacturers’ profitability. Separately, the consumer pressure on FMCG brands to be more sustainable is only increasing.
Where once consumers used to equate the concept of sustainability just with packaging and recycling, now their awareness also includes the natural resources used during manufacture.
Combine both of these factors and it’s no wonder that manufacturers are actively examining the sustainability of their manufacturing processes and urgently looking for new ways to reduce their consumption of natural resources like gas, electricity and water.
But it’s not always obvious how best to reduce resource consumption during manufacture without affecting the final product quality.
What can be done about it?
The article recommends an approach to investigate your manufacturing process and unlock sustainability improvements, focusing not on the resources that end up as ingredients or materials in the final product, but those used for heating, washing and other processes.
More sustainable manufacturing
The motivation for manufacturers to increase sustainability is generally for two reasons:
- To help reduce environmental impact either from carbon emissions or by-products such as waste water. As the world faces the challenge of drastically reducing emissions and consumption of natural resources, manufacturers need to play their part
- To counteract increasing operating costs for energy, water, or other consumables
Many manufacturers have set themselves tough challenges to reduce natural resource consumption, driven by one or both of the two factors above. But the relative importance of each factor depends on the situation in question:
Environmentally driven: where the aim is often to reduce resource use as cheaply and quickly as possible. Though the emphasis is to achieve genuine results, manufacturers will still be cost sensitive and desire minimal impact to the bottom line.
This means that any process changes shouldn’t decrease throughput or increase scrap rates, though one-off CAPEX costs might be acceptable.
- Operating cost-driven: where the benefits of reductions in these situations are simpler to judge, given that cost is easier to account for. But the environmental impact is a useful by-product for corporate social responsibility and marketing purposes, although it is a less tangible benefit
As manufacturing consultants, 42 Technology has worked with several FMCG brands who have revisited sustainability initiatives over time with an evolving justification. On one recent project for a widely successful consumer product, the focus several years ago was to achieve a purely environmental improvement without any expenditure.
But now, in the face of urgent consumer pressure, there is a larger budget for more significant process alterations. And the recent rise in energy prices has only compounded this, reducing the payback period for expensive improvements and resurrecting options that were once unviable but are now worth investment.
Unlocking resource savings
When it comes to identifying where reductions can be made, the most obvious step is to tweak the process parameters without making changes to the higher-level process steps or equipment setup.
But for most established processes, this evolutionary approach is likely to only yield small improvements. The optimum situation might have already been reached for many mature production processes or has been limited by the technologies used.
Going a step further to unlock significant savings requires a different mindset where it’s important to approach the problem in a more analytical and structured manner.
Understanding current process
First you need to know exactly where and how resources are used. It’s important to acknowledge any preconceptions you may have about how your manufacturing process operates, how resources are used, whether any can be reused, and most importantly: what parts of the process can and can’t be changed.
Making sure you’re approaching the task with an open mind, otherwise you might overlook good solutions.
The next step is to work your way through the process from start to end, noting where, and crucially, how resources are used. For example:
- Electricity is commonly used for heating and cooling, general machinery operation, and for motion or transport
- Gas is used for more cost-effective, high-power heating, but also increases local absolute humidity when burnt
- Water can be used for adding, removing, or transferring heat, washing ingredients or equipment, diluting chemicals, and for transporting solids in pipes
- Air, which can be considered as a natural resource, often incurs some expense to control its temperature or humidity
Be wary that when reviewing each process step, ideas for obvious process changes will inevitably stand out. But while these often seem like a great local solution, thinking at the system level might uncover the opportunity for even more impressive gains.
One example we have seen in a food industry process, was where the product was cooled, then much later heated. The best option was at the system level: a heat exchanger linking both steps.
To avoid missing these system-level gains, especially for areas such as heating and cooling, construct a flow diagram of the entire process to show the resource flows at each process step.
For resources like water or controlled air, this diagram makes a great springboard for inspiring powerful ideas such as rerouting flows of waste air/water to other process steps where requirements are looser.
Understanding resource use
It may appear obvious how a resource is used, but if you overlook any secondary functions, then you risk unanticipated consequences with any work to reduce resource consumption.
Two examples of ‘dual purpose’ resources we have experienced are:
- Gas – for heat and humidity
If you’re using gas for direct heating within an enclosed setting, remember that the combustion will add water vapour to the surrounding air. If you solve the heating problem (for example by installing electrical heating elements) then you should verify the impact that lower humidity air will have and increase it if needed.
This may be especially important in some food production processes, such as baked goods that are cooked in open moulds over flames.
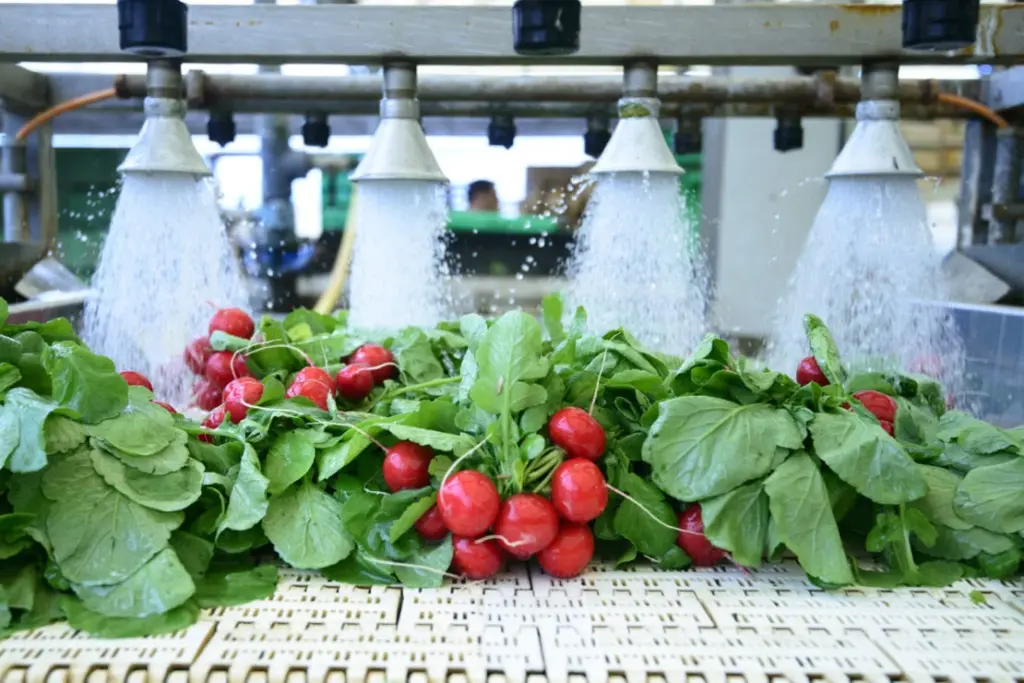
- Water – for washing and thermal transfer
If water is used for washing ingredients to remove contaminants, it will also act as a heat exchanger, heating or cooling the ingredients as the water flows past. It may be easy to miss that you’re currently relying on this action to get ingredients to a suitable temperature for a downstream process step.
So, if you manage to somehow make cleaning more efficient, you’ll also need to make sure that the rest of your process can tolerate colder/hotter ingredients, otherwise you may have to add more water back in to fix the process.
Generating ideas
Once you understand the resource use throughout your process, you can build up a menu of ideas with a range of potential savings. Initial analysis or lab testing will let you assign estimates for costs and benefits to each of these.
Your list is likely to range from cheap, simple optimisations (e.g. adding insulation and reducing heating power) to more complex redesigns (e.g. upgrading the least efficient part of the process) or complete system changes (e.g. linking separate process steps to reuse waste heat or water).
Selecting the best ideas
Few improvement initiatives can be made without securing budget or buy-in from within the business. A sensible development plan is crucial to getting this buy-in, including an estimation of the risks of the leading ideas, and how they will benefit the manufacturer’s sustainability objectives of either reducing operating costs or environmental impact.
Selecting the best ideas for further development does not necessarily mean selecting the ideas with the highest potential resource savings as these might be risky with obstacles obvious to the team. Instead, less risky ‘lower hanging fruit’ ideas might be the best way to go. It all depends on the specific circumstances.
Top tips for improvements
The issues discussed above are all fairly obvious when you take a step back, but all too often we have seen otherwise well-intentioned sustainability initiatives miss key solutions and deliver limited results for entirely avoidable reasons.
If you are planning a sustainability initiative, it’s worth considering the following top tips:
- Be clear about why you are aiming to reduce resource consumption — for environmental reasons or as a cost-reduction measure?
- Understand exactly how resources are being used in your current process. Gas and water in food and drink manufacture can have a surprising number of uses.
- Generate a selection of optimisation ideas and analyse their benefits. Which best suits your business case — inexpensive small mitigations or high development redesigns with huge potential?
Although the steps outlined above won’t take you all the way towards your sustainability goals, following a systematic process from the start will put you in the best place to make changes and to unlock genuine improvements.